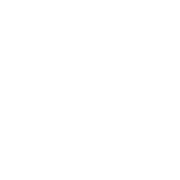 |
Message From the President-Elect
As an ergonomics practitioner and consultant, I have been challenged many times on projects to evaluate and provide solutions to complex problems. This has been very rewarding, but it also has challenged me to evaluate alternative approaches and my knowledge of our ergonomics science. One recent project that I would like to share involved the redesign and replacement of a new material handling system. During the demolition and construction phase of the project, the company created a temporary work area to allow operations to continue. This new area created a complex manual material handling (MMH) task. The job was made up of eight subtasks that included pulling, lifting, carrying, lowering and pushing objects of varying weights (ranging from 20 to 70 lbs.) hundreds of times over the course of the day. In addition to the MMH tasks, there was also reaching, back flexion, and walking, and the task was performed outside in a hot and humid work environment where temperatures could easily exceed 95 degrees.
The company was concerned about three things for this new temporary work area:
1)
What are the ergonomic risks of this job?
2)
How many objects can we expect employees to lift over the course of the day?
3)
Will fatigue be an issue and will employees get burned out?
To answer these questions let's take a look into our ergonomic toolbox and find some methods that can be used to provide management with some answers.
- Most of the ergonomic assessment tools evaluate single subtasks in insolation (NIOSH Lifting Equation, Snook/Liberty Mutual MMH tables, biomechanical software, Strain Index, RULA, HAL, etc.). However, most jobs involve more than one subtask, such as my example above.
- So, how do we assess the cumulative effect of multiple subtasks?
- Some current tools 1,2,3 that account for these type of activities involve using metabolic equations and work rates of each subtask, but they are very labor-intensive and time-consuming to use.
- Other methods have their own pros and cons and levels of complexity. These include: the NIOSH Composite Lifting Index (CLI)4; Cumulative Lifting Index (CULI)5; Cumulative Spine Compression and Shear6,7; Lumbar Motion Monitor8; Simulation Software (Jack Task Builder9); and, most recently, the Recommended Cumulative Rest Allowance10,11, Fatigue Failure Tools (LiFFT12 and DUET13), and the Three-Compartment Muscle Fatigue Model14,15.
As practitioners, we are often faced with workplace challenges that our ergonomic toolkit does not easily allow us to answer, so we rely on personal experiences and tradeoffs to provide our customers with the best solution based on the most accurate information we can obtain.
I want to start the conversation on this topic by hearing your thoughts on how you evaluate complex jobs. Please post your comments to the IISE Connect.
Stayed tuned for upcoming newsletters that will expand upon this topic!
|
Member Profile - Eric Hassen
Eric Hassen is Director of Business Development with
Caster Connection in Columbus, Ohio, where he has worked for six years. In this position, Eric and his colleagues work with engineers and ergonomists on a multitude of applications, many of which involve lowering the amount of pushing and pulling required to move materials handling carts.What Eric first found to be surprising about his job is the complexity of designing casters and carts to overcome the wide range of variables and obstacles that exist in an industrial environment. These features include caster bearing type and precision, the design of swivel leads, and the physical composition of the caster itself. He regularly works on challenging projects to meet customer needs, such as when an end user desires a cart design so that employees can safely push two tons of product! Eric finds it particularly satisfying when he can significantly lower push-pull forces of employees who must handle carts every day, knowing that this reduces their workload, makes their jobs easier, and results in a big improvements in their lives.
When not at work, Eric is active in the lives of his children, ages six and three. In the time left over, he loves to play golf, cook new dishes (as he once attended culinary school), and travel the world. His goal is to experience the many amazing things that exist in our world.
|
Profile: 2019 Winning Ergo CupĀ® Competition Entry - Honda of America Manufacturing
Tires used on Sport Utility Vehicles are heavy, and handling them manually is a risky practice. Associates who perform repair tasks at Honda's facility in East Liberty, Ohio were faced with routinely lifting tires weighing up to 67 lbs., often from floor to shoulder heights. Internal ergonomics evaluations determined this activity to place Associates at unacceptable levels of work exposure.
As a result, an internal team (the "Pit Crew") was formed to solve this concern. They found a decommissioned piece of equipment in the facility and modified it to position tires in place. The team also fabricated a ramp to allow Associates to roll the tire onto the tool, to eliminate all manual lifting throughout the repair process. This solution has eliminated all ergonomics-related risks! It addition, it helped prevent damage to parts, and Honda has found this fixture to have applications across the auto industry and beyond.
This solution was impressive enough to win the Ergo CupĀ® for Team Driven
Workplace Solutions with Internal Competition at the 2019 Applied Ergonomics Conference, held this part March in New Orleans.
Congratulations!
If you would like to know more about this innovative solution, contact Jose Banaag.
|
The Ergonomics of Driving
Whether a professional driver or just a commuter, most people drive as a part of their daily routine. Also, as summer approaches, many of us will be taking long road trips as well. When it comes to knowledge about safe driving, most people tend to think of precautions to avoid crash-related accidents and injuries, such as securing seat belts, avoiding distracted driving, ensuring proper tire tread and pressure, adjusting speed for the road conditions, etc. However, given that the average commuter spends the equivalent of roughly nine days a year (or 31 days a year for our mega (90 minutes one-way) commuters!), the ergonomics of driving should be a primary topic as well when it comes to driver safety.
An inadequate vehicle/driver set-up can lead to static awkward postures, resulting in a range of ailments, from mild discomfort to diagnosed musculoskeletal disorders (MSDs). A study conducted by ebay Motors in the UK found that nearly half of drivers suffer from repetitive driving injury (RDI) such as foot cramps, low back pain, stiff neck, and headaches. Many of those surveyed exhibited signs of an RDI within as little as 15 minutes of driving! In addition to an increased risk of discomfort or an MSD, a poor set-up can also impact one's ability to see clearly (out the windshield and side mirrors) and can increase fatigue, which impairs one's driving ability and reaction time.
READ HERE tips to consider when training your employees, or educating yourself, on the ergonomics of safe driving.
.
For more information on driving ergonomics check out the free
online training course offered by the Washington State Department of Labor Industries.
|
Opportunity to Increase Your Ergonomic Connections
Are you dealing with an ergonomics concern and looking for advice? Do you have questions about how some possble ergonomics solutions have been implemented elsewhere? Or, would you like to boast about an ergonomics success you've implemented? One way to communicate with others who have a wide range of insights and backgrounds is to post on
IISE Connect
. This platform allows users to discuss topics of interest and seek feedback and guidance. Even better, IISE Connect is included in your AES membership!
|
New Applied Ergonomics Research on Exoskeletons
- A Field Evaluation of Arm-Support Exoskeletons for Overhead Work Applications in Automotive Assembly
Occupational Applications
: The results of this field trial suggest that when made available for optional usage during overhead automotive assembly, arm-support exoskeletons can lead to a substantial decrease in self-reported musculoskeletal discomfort in the neck and shoulders. Participants (assembly operators) chose to use the device for 86% of their shift and indicated they would continue to use it daily if provided the opportunity. The results of this investigation suggest that when used alongside a traditional proactive ergonomics program, arm-support exoskeletons may reduce some risk factors associated with the development of shoulder injuries. The approach presented may be useful for practitioners that are starting to explore arm-support exoskeletons in their workplace. Several areas of improvement were highlighted for future design consideration, including further reducing weight and improving thermal comfort. GET MORE INFORMATION
- Potential of Exoskeleton Technologies to Enhance Safety, Health, and Performance in Construction: Industry Perspectives and Future Research Directions
Occupational Applications
: Work-related musculoskeletal injuries and disorders remain an important problem in the construction industry. Exoskeletons are an emerging wearable technology that assists or augments a user's physical activity or capacity. This technology is a potential solution to reduce the physical demands and fatigue experienced by construction workers and help improve worker safety, health, and performance. As a first step towards enabling exoskeleton use in construction, we captured the perspectives of construction industry stakeholders regarding adopting exoskeletons and continued use in practice. Stakeholder responses highlighted several important questions and concerns, which were grouped using qualitative content analysis into three categories: (1) expected benefits, (2) exoskeleton technology adoption factors, and (3) perceived barriers to use. Uncertainties were expressed about the practical value and usability of exoskeleton technologies, and the impact of this technology on worker safety. Given this, and the limited state of current evidence, we summarize important research gaps that need to be addressed in future for successful adoption and use of exoskeleton technologies in the construction industry. GET MORE INFORMATION
|
AES Corporate and University Partnerships provide exceptional value
* Corporate Partners can affordably develop staff and get them the training
necessary to optimize the enterprise.
* IISE University Partners boost their faculty's opportunity to network and
publish research.
* IISE tailors your Corporate or University Partnership to address your
organization's unique needs.
* Contact
Doug Long
, IISE's Global Director, Strategic Alliances, at
[email protected]
or
(770) 349-1109
to learn more.
|
Do you have any ergonomics-related insights you would like to share with other AES member in this newsletter? Or, do you have a topic you would like to see explored in more-depth in a future issue? If so, please contact
IISE
.
|
AES Newsletter Team: Gary Allread, Editor and Bobbie Watts, Co-Editor
|
|
|
|
|
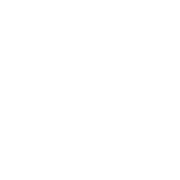 |