Tank over-vacuumization: Unintended consequences of decommissioning Stage II vapor recovery systems
By John Albert, Program Administrator-Petroleum/Propane/Anhydrous Ammonia, Missouri Department of Agriculture, Division of Weights, Measures, and Consumer Protection
About two years ago, I had an experience during a training session at a convenience store in Missouri. Picture this: The site has 1987-vintage sti-P3 tanks with single-walled fiberglass lines, a coaxial delivery system, a flapper valve, an Incon tank gauge, and CARB- approved pressure/vacuum vent valves on each vent line. The owner/operator is diligent about compliance.
When I tried to remove the fill cap from the unleaded tank, I could barely get it off
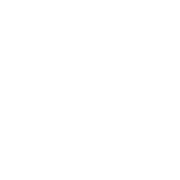 |
|
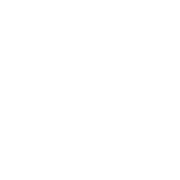 |
John Albert finds it necessary to pry off a vent cover.
|
due to the extreme vacuum inside the UST. Once I was able to remove the cap, we could hear the tank creaking and popping as it "breathed in." I purposely timed how long it took for the pressure to equalize--it was a full 45 seconds!
Several experienced emergency responders participating in the training were astonished and very concerned about stress on the tank that was occurring because of repeated deformation caused by "release and breathing" each time the fill cap was removed. Without exception, they expressed concern that this situation--caused by vapor recovery air pollution rules--could actually be increasing the risk of UST failures and leaks.
Unintended consequences In May 2012, the Environmental Protection Agency (EPA) issued their "Widespread Use Rule" which determined that on-board refueling vapor recovery (ORVR) had penetrated the highway motor vehicle fleet sufficiently and that Stage II vapor recovery had become redundant and unnecessary. In fact, it was posited that because of the number of ORVR vehicles now on the road, Stage II may be causing more harm than good. This rule led states' air pollution programs to decommission gasoline dispensing facilities (GDFs) in accordance with their state implementation programs.
However, not long after decommissioning had started, field inspectors began reporting difficulty removing fill caps to return test fuel after device accuracy tests. In some cases, a pry bar was necessary to remove the cap, followed by a long period of inhalation, with audible tank distortion. It was clear that the decommissioning of Stage II equipment was causing significant negative internal tank pressure. Station operators also began to report false ATG readings that returned to normal upon opening the fill cap to relieve vacuum in the head space.
Owners concerned about gauge accuracy drilled small holes in the ATG drop tubes to allow the liquid level to equalize. Some simply left the fill caps loose to prevent vacuum build up. One owner of multiple stores loosened all pressure/vacuum vents after they were tested each time. All of these owner strategies sacrificed air quality, but potentially prevented ground water contamination.
Those of us in Missouri became greatly concerned about possible tank damage and/or implosion that could be an unintended consequence of increased negative internal tank pressure after decommissioning Stage II vapor recovery systems.
Altering the consequences All pressure vacuum vents must be CARB approved. However, approved models have a very small inlet, making it difficult for internal and external pressures to equalize, especially at high throughput facilities. The Missouri Department of Agriculture worked with PSTIF, DNR, tank owners and vent manufacturers to develop a study of non-CARB approved vents with larger less restrictive inlets. When we installed these P/V vents in multiple locations, both inside and outside the non-attainment areas, we found that they alleviated the over-vacuumization problem.
Missouri has completed testing pressure vacuum vents for collection efficiency at three separate locations. Missouri DNR has agreed to allow the use of vents that are not CARB approved as long as they can pass the decay test and prove 98% collection efficiency during transfers.
Compared to other areas of the country utilizing Stage II vapor recovery, Missouri was unique. Missouri Stage II facilities were using a simple balance system--fuel left the storage tank and entered the vehicle while an equal amount of air was returned to the storage tank. This is no longer the case, now that decommissioning of Stage II has been completed. Other states had opted for vapor assist or other power-assisted vapor return systems. Regardless of the system design, this is clearly a problem that needs to be addressed.
Until a feasible solution is found, tanks will continue to be in jeopardy from over-vacuumization due to Stage II vapor recovery decommissioning. In Missouri, it is our hope to use non-CARB vents that meet DNR's specifications as a solution that can be used by other states .
|
STI-SPFA's Product, Quality, Safety awards for 2016
STI-SPFA's members are proud to fabricate the best in steel plate products. Each year, we recognize their efforts with our award programs.
Quality Awards
Quality control is a crucial aspect of all manufacturing processes. Member fabricators of the Steel Tank Institute's licensed tank technologies are subject to periodic, unannounced inspections by a team of STI-SPFA Quality Control Inspectors. These inspectors conduct a rigorous investigation of the manufacturing function at tank fabricator facilities, to ensure that companies are complying with the standards and specifications for manufacture of each licensed technology.
Safety Awards
STI-SPFA and its members value the safety and health of their employees, customers, communities, and the environment. Since 2003, STI-SPFA has annually recognized the safe performance of members' fabrication and field operations. Safety Awards are presented annually to acknowledge the highest achievements in the safe performance of companies engaged in shop fabrication, inspection, maintenance, and field construction activities.
Both the Safety Award of Excellence and the Safety Award of Achievement represent masterful achievements, as employees routinely work at heights, bend and weld inches-thick steel, pressurize vessels to withstand hundreds of pounds of pressure, and maintain everything from refineries to water reservoirs.
Product Awards
STI-SPFA's Annual Product Awards recognize the steel construction products made by our members that exemplify the best of the steel fabrication industry. These projects demonstrate the positive qualities and flexibility of steel as the production material of choice for many products in many industries.
For the 2016 Product Awards, there were 49 entries in 14 categories from STISPFA member companies, utilizing a total of 38,325 tons of steel. To determine the winners, all association members assessed each entry by anonymous ballot, based on four criteria: promotional value, uniqueness of product, design and engineering, and aesthetics.
Back to top
|
Steel Facts: Coatings and linings for water storage tanks
STI-SPFA recently published the latest in its series of Steel Facts documents.
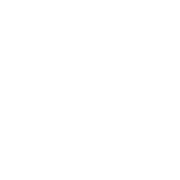 |
|
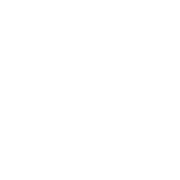 |
See this artful steel tank coating! |
"Coatings and linings for water storage tanks" presents information on the corrosion resistance, durability, impermeability, flexibility, and quick cure rate of today's coatings and linings.
"Coatings and linings for water storage tanks" is the eighth in the Steel Facts series, all developed by industry experts and referenced to credible sources:
Back to top
|
Trump's EPA cuts could negatively affect OUST
President Trump's proposed budget could have serious impact on the Office of Underground Storage Tanks (OUST). EPA's "2018 Budget in Brief" document notes:
- Eliminates Categorical Grant: Underground Storage Tanks (FY 2016 budget $1.498 M). The program provides funding for petroleum and hazardous substance release prevention and detection activities including: compliance assistance, state program approvals, and technical equipment reviews and approvals.
- Eliminates LUST Prevention (FY 2016 $25.369 M). The program provides resources to states, tribes, territories, and inter-tribal consortia for their Underground Storage Tank (UST) programs, with a focus on inspections, enforcement, development of leak prevention, regulations, and other program infrastructure.
- Reduces LUST Cooperative Agreements budget by 29% (2017 $54.935M to 2018 $38.840M): LUST funding supports states in managing, overseeing, and enforcing petroleum cleanups at LUST sites.
- Reduces EPA agency expenses budget (FY2017 $11M to 2018 $5.6M): EPA's own funding for salaries and administrative expense. EPA employs staff in policy development, research, policy interpretation, and outreach activities, for example.
While the President's budget has a long way to go through Congress, these proposals in the EPA portion must be carefully watched.
Back to top
|
STI's USTs can be buried to any depth
Steel's strength and versatility are well known. Steel tanks can be manufacturered in any size, any configuration, and as single wall, double wall, or even triple wall tanks.
One of the unique attributes of a steel underground tank is that it can be buried at any depth: the maximum burial depth increases or decreases simply by changing attributes such as diameter, length, steel thickness, number of walls, internal compartments, and so on.
To determine the proper thickness of steel for a particular tank depth, the fabrication industry uses the Roark formula. It was chosen based on innovative, extensive research by STI in cooperation with Underwriters Laboratories. Testing was conducted on full-size tanks.
In the Roark formula, burial depth is directly related to steel thickness or stiffness of the tank. Because steel tanks are designed to this formula, the tank manufacturer has wide flexibility in both design and burial depth of the tank, allowing tank owners to specify the options they want and need.
In contrast, fiberglass reinforced plastic (FRP) tanks are tested to only a single, maximum depth, limiting their options.
For further information, contact
Lorri Grainawi, STI Director of Technical Services.
Back to top
|
"One of the smallest chemical plants responsible
for one of biggest clean air success stories"
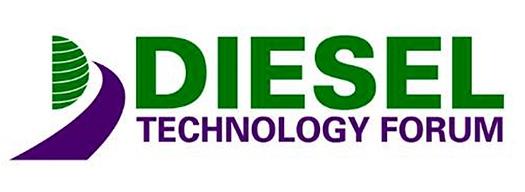 That's the headline of an April 7 article from Diesel Technology Forum, a non-profit organization dedicated to raising awareness about the importance of diesel engines, fuel and technology.
"According to the U.S. Environmental Protection Agency (EPA), the largest sources of emissions of oxides of nitrogen - NOx, a smog-forming compound - are attributable to large heavy-duty commercial vehicles.
"However, over the next 20 years, the largest
reduction in emissions of oxides of nitrogen will be attributable to commercial vehicles. The greater adoption of a clean diesel technology called Selective Catalytic Reduction is largely the contributing factor to this emission reduction success."
Here's a graphic of how Selective Catalytic Reduction works:
Further, according to the Diesel Technology Forum, "A recent report issued by the U.S. Department of Transportation confirms that one ton of NOx emission reductions can be achieved by investing only between $13,000 to $77,000 in a new diesel engine in a variety of commercial vehicles. In contrast, one ton of NOx emission reductions reqiures an investment in $1.4 million in electric vehicle charging infrastructure."
Back to top
|
sti-P3 cathodic protection procedures revised
STI recently issued a revised
Recommended Practice for Testing Galvanic Cathodic Protection Systems, R051. The document is available from the
STI-SPFA Store.
The revisions were developed by a balanced committee consisting of regulators, cathodic protection experts and testers, tank owners and tank manufacturers.
A number of significant changes were made:
- A form was developed for testers to report their CP test evaluation. The form can be used for tank, pipe, and flex connector test results and is similar to many of the state forms currently in use.
- Drawings were added to the RP to make it easier to use.
- A procedure was added for testing flex connectors with cathodic protection.
- A definition section was added.
- The section on remote reference cell readings was worded to clearly define this term, and step-by-step guidelines were added to define "true" remote earth.
STI would like to thank our committee members, who dedicated considerable time and thoughtful effort to help improve R051 for everyone to use:
- William Simpson, CP Specialist, PCA Engineering, Inc, NJ
- Rick Rogers, CP Specialist, UST Corrosion Management, SC
- Steve Nagy, CP Tester, Tait Environmental, TX
- Kevin Henderson, CP Tester/consultantr, Kevin Henderson Consulting, LLC, MS
- Tim Sievert, CP Specialist, Advanced Corrosion Control Technologies, WI
- Ed Ward, Contractor, SC Fuels, CA
- Brian Pottebaum, Insurance, R&A Risk Professionals/PMMIC, IA
- Matthew J. Cutshall, Owner, Sheetz, Inc., PA
- Eric M. Swaisgood, Owner, Speedway LLC, OH
- Bob Pickens, Owner, AT&T Services, Inc., TX
- Michael Pomes, Regulator, US EPA, KS
- Stephen Pollock, Regulator, VA DEQ, VA
- Mike Asma, Regulator (alternate), VA DEQ, VA
- Michael Phelps, Regulator, NC DENR, NC
- Andrew J, Koenig, STI member, Enerfab, OH
- Mike Hill, STI member and CP tester, Mass Tank Inspection, MA
- Coby Hayes, STI member, Committee Chair, JL Houston, MO
Back to top
|
ULC considers climate change impact on infrastructure
UL-Canada (ULC) Standards is working with the National Research Council of Canada (NRC) to study possible changes that may need implementation as part of the Government of Canada's program to protect the resilience of Canada's infrastructure from the effects of climate change.
It is anticipated that the results will yield new values for the intensity of temperature, wind, rain, snowfall, flooding, seismic events, etc.
In other news, ULC and UL are working together to develop a bi-national standard for fiberglass reinforced plastic underground storage tanks storing petroleum fuels. A committee is well into the process of developing the first draft which will be vetted through the full UL CSDS ANSI process.
Back to top
|
Water, water everywhere...and corrosion...and sludge....
As long ago as 2005, petroleum giant BP warned about the effects of water on diesel fuel storage. Under normal circumstances, diesel only remains in usable condition for 6-12 months. In an informational brochure, BP notes factors that "accelerate aging" of diesel fuel and what do to about it:
- "The presence of water. Water allows the growth of fungus and bacteria, these produce natural by-products such as organic acids which make the fuel unstable.
- "Establish a regular fuel maintenance program to ensure that water and dirt is removed from storage tanks. This will also remove any chance for fungus to grow.
- "Water should be drained from the storage tanks weekly. The frequency can be extended if the tank shows no tendency to collect water but should be done at least monthly."
These days, of course, there's a great deal of talk about water in storage tanks and
resulting fuel problems, particularly with ultra-low sulfur diesel (ULSD). Instances of corrosion of internal tank fittings and development of sludge due to microbial activity have been in the news for the past few years. These photos show examples:
|
|
|
Sludge in FRP diesel tank bottom
Photo courtesy Refuel Environmental Svcs
|
|
|
Same FRP tank after cleaning
Photo courtesy Refuel Environmental Svcs.
|
|
In July 2016, EPA released its study of corrosion in ULSD storage tanks and found it "nearly everywhere." (EPA's study results indicate only to what extent this corrosion of storage tank internal components may be occurring. These results do not imply that the tank system and/or the owner/operator are at fault.)
At this time, the cause of corrosion in tank systems storing ULSD remains unknown. Further research is underway by the Coordinating Research Council (CRC), a nonprofit industry group which works "to develop the best possible combinations of fuels, lubricants, and the equipment in which they are used." To our knowledge, the EPA has no plans to independently pursue research, but will continue to cooperate with and contribute to CRC's efforts.
Back to top |
STI clarifies: You've got options!
There's a lot of emphasis on removing water from storage tanks lately, because newer fuels appear to be strongly affected by water. And while it's always been the case that tanks can be built with options, STI has recently added language to its specifications to make it clear that s
teel storage tanks can be built with various options, such as:
- A fitting on the primary tank for the purpose of removing water bottoms.
- Additional openings on the interstitial space for the purpose of removing unintentional fluids.
- Triple-walled tanks.
STI strongly urges tank owners and operators to establish regular and frequent tank inspection, and to promptly remove any water present.
Get this FREE document from the STI-SPFA website:
Back to top
|
Trump's Commerce Department to investigate steel dumping
On April 20, President Donald J. Trump called on Secretary Wilbur Ross to prioritize a Department of Commerce investigation into the effects of steel imports on US national security. The study will consider overcapacity, dumping, illegal subsidies, and other factors, to determine whether steel imports threaten American economic security and military preparedness.
If any national security threats from steel imports are identified, recommendations for next steps will be reported. Under Section 232 of the Trade Expansion Act, the President has broad power to adjust imports-including through the use of tariffs-if excessive foreign imports are found to be a threat to US national security.
For example, the US military often needs specialty steel alloys that require unusual production skills and are used for armor, vehicles, ships, aircraft, and infrastructure. As a result, a robust and healthy domestic steel production industry may be deemed necessary to guarantee military supply chains in the event of conflict.
The United States is relatively unusual in that it has no tariffs on steel but has had to impose anti-dumping or countervailing duties in over 150 cases, with 13 more currently pending. However,
the US steel industry has struggled in recent years: i
ndustry employment has been declining, companies are highly leveraged, and businesses remain both capital intensive and lacking strong cash flow. Imports now represent 26% of the market and the US steel mills and foundries are operating at just 71% of capacity.
In a speech on Monday, May 22, Secretary of Commerce Wilbur Ross stated that there is massive global steel capacity due to over-production. Maximum employment at the steel mills in China results in dumping of steel in other countries, with the United States as a primary target.
The Commerce Department reports that it has countered with 392 anti-dumping cases, 191 of them steel-related and with China involved 40% of them. According to Ross, only 2% of imported freight is inspected, resulting in billions of dollars in duties uncollected at the US borders.
Fabricated steel products, such as pressure vessels used in the petrochemical industry, are also being imported. Because they are made overseas, they are cheaper and are depressing the market for pressure vessels made in the United States.
In its investigation, Commerce will try to determine if Americans are losing jobs as a result of the dumping of steel into the USA, and whether American prosperity and security is impaired. Questions to be considered are whether corrective tariffs should be imposed on all countries who import steel; and what action mikght be taken with NAFTA countries, from which 26% of all steel is imported.
The statutory timeline under the Section 232 provision is a maximum of 270 days, but Secretary Ross said says President Trump wants results more quickly.
Back to top |
|