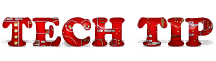
Mission recommends
performing a bi-annual system test of each RTU to verify the monitoring system is operating as expected.
Tests can be done on the high level floats, digital and analog inputs, tank and well control, intertie, backup battery capacity, and more.
For more information, please read our Spring Cleaning & Fall Fix-Up Service Bulletin found under the downloads tab of your web portal.
If you have any questions regarding Spring cleaning, please contact Mission Technical Support at (877) 993-1911, option 2.
|
|
Tradeshows
April 3-5
June 12-14
Philadelphia, PA
Week 4: Web Portal II - Supergraph, Reporting, Volumetric Flow, and Advanced Topics
Week 5: Special Topics
Week 1: Survey of Features
Week 2: Hardware, Instrumentation, and Installation
Week 3: Web Portal I - Notification and Unit Setup Options
Week 4: Web Portal II - Supergraph, Reporting, Volumetric Flow, and Advanced Topics
Week 1: Survey of Features
Week 2: Hardware, Instrumentation, and Installation
Week 3: Web Portal I - Notification and Unit Setup Options
Week 4: Web Portal II - Supergraph, Reporting, Volumetric Flow, and Advanced Topics
Week 1: Survey of Features
Week 2: Hardware, Instrumentation, and Installation
|
|
|
Mission Rolls Out OPC UA
Connection Method
|
Managers of larger wastewater treatment or water processing facilities sometimes prefer the data collected by Mission to be included with the client/server SCADA HMI that is part of their plant operations. Mission has provided this service to customers via the Classic OPC connection method for over 10 years. We are pleased to announce that we have released the newest connection method known as the OPC Unified Architecture. Our OPC UA connection is based on the latest standard (v 1.03) from the OPC Foundation. No Mission software is required on-site because the OPC UA Server runs remotely within the secure Mission infrastructure.
What is OPC UA?
OPC UA is an industrial communication protocol developed for process control and is the successor to the OPC Classic protocol. It offers better security, stability, and software support with added features like multi-platform support. OPC UA simplifies connections because it no longer depends on legacy Microsoft COM/DCOM technologies. The new protocol also makes firewall client-side configurations much easier.
Advanced Multilevel Security
OPC UA offers extensive built-in security known as UA Secure Conversation. This includes:
- Authentication with X.509 certificates for both client and server before a connection is allowed.
- Session Encryption where all messages are encrypted with 128 or 256-bit encryption before transmission.
- Message Signing meaning all messages are signed to ensure they are received exactly as they are sent.
- Sequenced Packets to reduce opportunities for message replay attacks.
- User Access Control which requires user authentication before a connection can be established. It further restricts access to individual data nodes.
- Auditing and Logging of all user activities.
How Do I Connect to OPC UA?
A native UA Client that is a component or plug-in to the HMI is the recommended way to connect to the Mission OPC UA Server. Most UA clients offer advanced UA features such as multiple timestamps, function calls, or commands.
For existing Mission OPC clients and HMIs without a native OPC UA client, a third-party middleware called UA Proxy can be used to translate data between the OPC UA server and OPC Classic client. This can be obtained from multiple manufacturers. The following UA Proxy solutions have been tested and verified to work with the Mission OPC UA Server:
- Kepware KEPServerEX 5
- Matrikon MatrikonOPC UA Proxy
- Unified Automation UaGateway
What Can It Do?
Up to 240 data points (based on RTU configuration) per RTU are sent to your SCADA-HMI once an OPC UA connection is established. These include:
- Digital inputs: labels and state
- Digital outputs: (relay outputs) labels and state
- Analog input: labels, absolute values, and scaled values
- Hourly and daily information such as pump run, number of pump starts, flows, and rainfall information
- Battery and AC Voltage
- Count of Unacknowledged alarms
- Many more enhancements
RTU data is continuously stored on the Mission data servers so the Mission web portal is always available for viewing, configuration, and other functions. Some OPC users use Mission for telemetry and their SCADA-HMI for alarming and reporting. Others take a hybrid approach where alarm callouts and acknowledgments are performed by Mission and their traditional system functions as a historian. Other managers use Mission as a "warm" backup system and only enable Mission alarm callout functions when they are needed.
Current OPC customers can take advantage of this new technology now. For questions or more information, contact OPC@123mc.com
|
Distributor Conference
a
Great Success
|
|
Mission welcomed about 50 of our distributors to Atlanta on Presidents Day this year for a new product and services training conference. The event was an overwhelming success and we were delighted to see representatives from as far away as California and Quebec. Attendees were able to see some of our newest technologies, a demonstration of our new web portal, and tour our brand new facility. Here are some highlights from the conference:
|
Forrest Robinson i
ntroduction to the Distributor Conference with a market overview
|
Conference Takeaways
The conference started with a brief state-of-the-market overview by Mission President Forrest Robinson that included these facts:
- The pace of new customer additions has increased and Mission now provides Managed SCADA service to over 2,400 utilities.
- Our reseller family is healthy with an average relationship of over eight years.
- Resellers who specialize in instrumentation and municipal pump systems use Mission products and service to improve overall efficiencies.
The Live Debut of 123SCADA.com
With the help of Tania Espadas, Paul Nappo
presented our
new state-of-the-art web portal, 123CADA. 123SCADA features an enhanced website desktop that works with any modern web browser without requiring any software installation. It uses the same TLS security that protects online banking transactions to ensure encrypted, secure access. Customers can access the site now by logging in as usual and clicking the beta graphic icon to the right of the screen. The 123SCADA Introduction video explains the new web portal enhancements.
More Conference Highlights
- Senior Electrical Engineer Robert Burke premiered the new MyDro Remote Terminal Unit. The MyDro is designed as a highly reliable, economical and easy-to-install RTU that is built for a long service life. Robert highlighted the numerous enhancements that ensure the MyDro family of RTUs is well received.
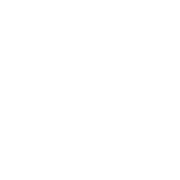 |
|
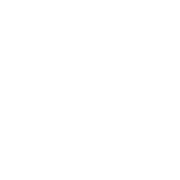 |
MyDro |
- Forrest Robinson reported the MyDro RTUs will be available in the second quarter of 2017. He reminded everyone that the Mission Technology Obsolescence Guarantee is available for users interested in upgrading an M110 or M800 RTU to the new MyDro M150 or M850.
- The Mission Sales team led by Matt Croussillac covered many applications in detail. Matt said it is very useful for distributors to learn the many other ways Mission is being utilized throughout the U.S. and Canada.
- Joe Robinson discussed a number of experiences our Technical Support Specialists typically encounter. He pointed out that jobs that start well are more likely to go smoothly and end well. He emphasized it is extremely helpful for support specialists to understand customers' unique requirements and have site surveys and contact information to serve them more efficiently.
- The conference was rounded out with a tour of our brand new facility that is designed to assist with training and collaboration.
|
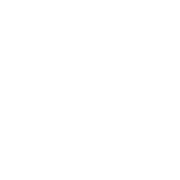 |
Mission hosted dinner for both the distributors and staff during the conference. |
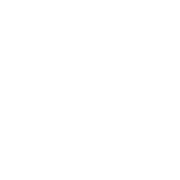 |
Jim Davis of AWC, Inc. was especially enthusiastic in our post-conference survey. "The conference was great! Mission has always been a forward-thinking company," wrote Davis. "They have continuously been able to set the bar higher for new product offerings and have delivered on their promises to provide unique and technically advanced products which fit comfortably in the marketplace. Out of all our manufacturers we represent, Mission has remained at the top of the list for technical, customer, and sales support."
|
Mission Makes the Move
|
Mission has experienced tremendous growth in recent years not only in our customer base but our staff as well. All of this growth meant we had outgrown the facility where we have been for over 12 years. We realized it was time to move to a bigger and better place. After months of searching, the perfect building was finally located and high-tech renovations began. We officially moved in on the first of February.
Designed for Total Collaboration
Our building is not only beautiful but ergonomic and spacious. The new facility is twice as large as our previous building with an intelligent layout that comfortably accommodates engineering, technical support, production, accounting and administrative staff. From the moment you enter the building, you will find it inviting, with a comfortable reception area complete with a beautiful saltwater aquarium soon to be monitored by Mission.
The entire facility is illuminated with warm eco-friendly LED lights and features anti-static flooring where appropriate. The new building is designed with total collaboration, efficiency, and team-building in mind so we can serve our customers even better.
Mission is very excited about our new building and would be pleased to give you a tour. We encourage any of our customers traveling through the Atlanta area to stop by and visit us.
|
In Memory of
Tom Glendinning
|
|
Tom Glendinning, a beloved member of the Mission family, passed away Friday, February 24th, 2017 after an extended illness. Tom served as technical support manager from 2008 until his promotion to general manager in 2015.
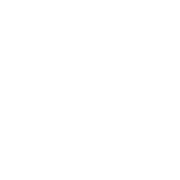 |
|
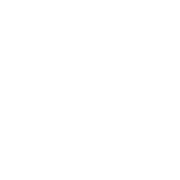 |
Tom Glendinning
|
Prior to joining Mission Communications, Tom owned and operated a security company in Savannah, Georgia. He had been a law enforcement officer in Florida earlier in his career. Tom is survived by his brothers William Downing Glendinning and Richard Norris Glendinning, along with several other family members.
Tom will be remembered for his technical expertise, discriminating palate, and quick wit. His sense of humor had you laughing from the moment you dialed his 1007 extension and heard the iconic 0-0-7 theme song until you hung up. When asked how he was doing he'd respond, "I was doing better but I got over it." If you thanked him for his assistance, he'd chuckle and say, "I'd like to say you're welcome but I ain't that big of a liar." Tom had the unique ability to provide a solution to a technical issue and at the same time make you laugh. Very few technicians could pull this off!
Tom put his heart and soul into everything he did and took great pride in his work. He left a permanent mark not only on the seat of his chair but in all of our hearts as well. He is greatly missed.
|
|
|